// Access Control & Identification
Securing Success in
Locks & Door Hardware
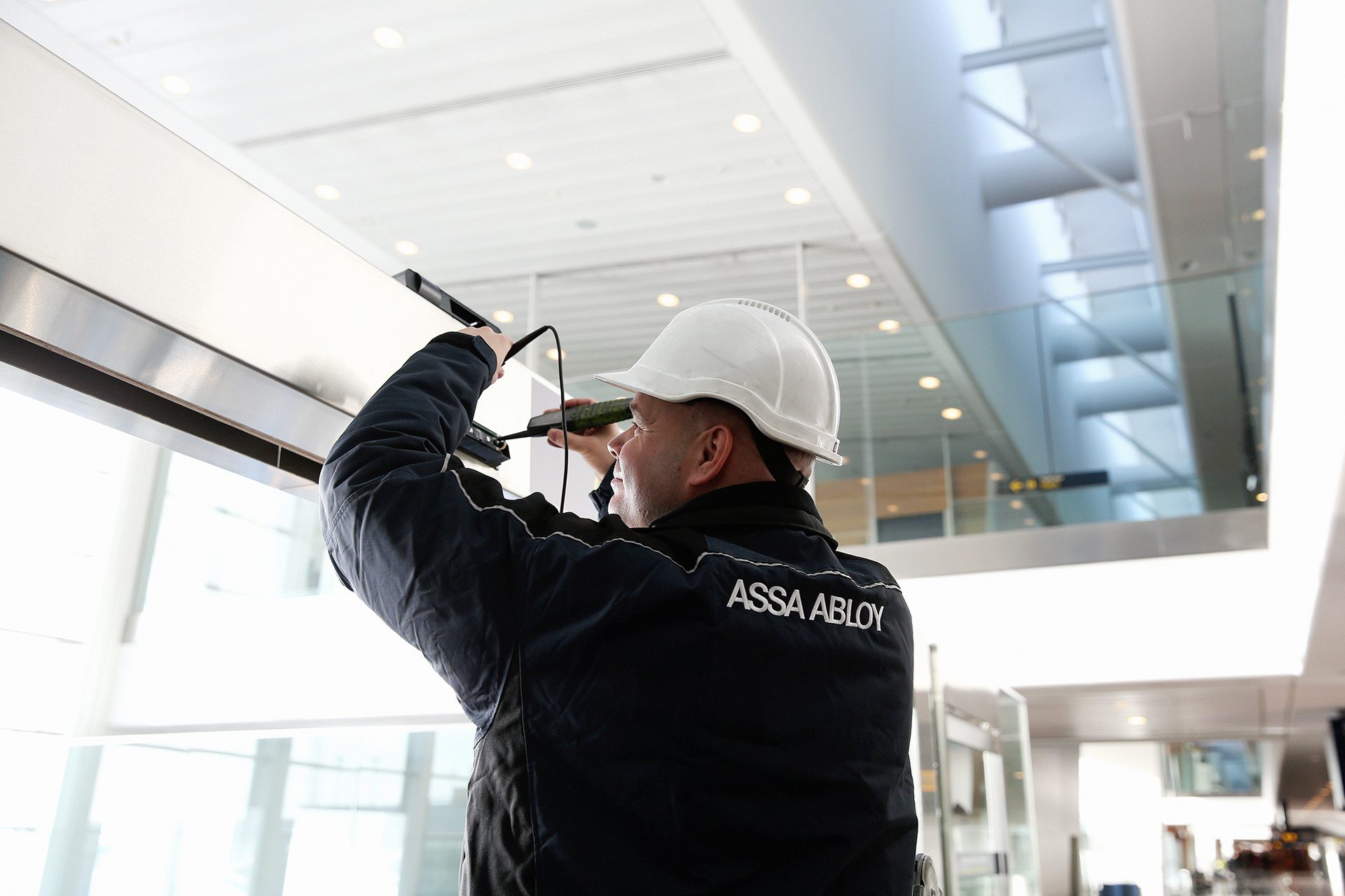
There are pros and cons to both in-house installation and repair and outsourcing the job. As for outsourcing, it can allow integrators to overcome labor shortages and focus on their core competencies.
IMAGE COURTESY OF ASSA ABLOY
Lock and door hardware experts weigh in on installation and repair pitfalls and how to avoid them.
By Christopher Crumley, SDM Staff Editor
Even though the mechanical industry of locks and door hardware has entered — along with the rest of the world — into the age of Wi-Fi and wireless, there’s still the physical need to install, repair and even retrofit existing solutions to meet end users’ evolving security needs.
“A typical wired opening consists of a number of discrete components around an opening: a locking device — whether it’s a strike, maglock or electro-mechanical lock — a wall reader, sensors for door position and request to exit, and so forth,” says Lester LaPierre, director of business development – electronic access control, ASSA ABLOY, New Haven, Conn. “All these discrete components are mounted around an opening. Often, these drops are required to be in conduit, which means involving multiple trades to install one opening.”
Wireless locks have made this somewhat easier, LaPierre adds. “With today’s intelligent wireless and Wi-Fi solutions, these components are integrated into a single locking device, which simplifies installation considerably. Instead of multiple trades taking six to eight hours for a single opening, trained and certified integrators can have an opening online in under an hour. The simplicity of today’s smart door security solutions also reduces points of failure and repair time since there are fewer components and far less wire involved.”
However, even with the increasing ease of installation some products offer, time and time again, security industry experts stress the importance of having an understanding of the doors you’re working on, the hardware they need, and the regulations that they are subject to.
Advice Avoiding Installation Pitfalls
Several experts interviewed for this article offered sage advice for security dealers and integrators on working with locks and door openings.
When it comes to training, there is sometimes a lack of understanding about door hardware, such as these door strikes from Camden that ensure the door latches when closed.
IMAGE COURTESY OF CAMDEN DOOR CONTROLS
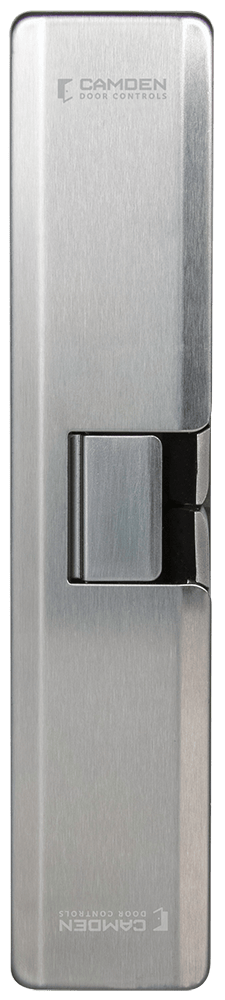
According a spokesperson from SDC, Camarillo, Calif., one of the most important elements of the lock and door hardware install is the power supply. “Based on more than 50 years of our manufacturing experience, 75-85 percent of access control operating problems and technical support calls are due to power issues,” the spokesperson says. “Linear power supplies have been used for years to power resistive, capacitive and inductive loads — devices with coils or solenoids, such as electromechanical and electromagnetic locks and strikes — due to their ability to handle large inrush currents. … However, the penalty in using a linear power supply is the heat generated by the regulator component of the supply due to its moderate efficiency. The heat generated can lead to early failure of the temperature sensitive components housed near to the supply board.”
Murray Lewin, senior product manager, access control solutions dormakaba, Indianapolis, Ind., says to keep an eye on which products you use. “We always emphasize using products that are well established and have appropriate certifications for the opening for optimal performance,” Lewin says. “These are actual certifications such as UL or BHMA that are listed on stickers placed on products or etched onto the product itself. Products that state they ‘meet the requirements for certifications’ but do not have the actual certification credential visible, are not typically tested to the same high standards of performance criteria.”
Talent Gap in Locks & Door Hardware
Some experts SDM spoke with expressed concerns over a talent shortage in the security industry — more precisely, the gap between some of the industry mainstays and the industry newcomers. “Our industry is such that even if you hire somebody, it takes them a while to really learn and onboard into their position,” says Yong K Lacy, Allegion. “That was the feedback that we were receiving even before, but it was more concerned around making sure, when some of the experienced workers and technicians retired, that we get the younger generation or even somebody new to the industry joining our market and help them onboard.”
NAPCO’s Peter Lowenstein adds, “There’s a 40- or 50-year age gap. The industry did not do a good job of preparing to replace themselves. Here we are in this crunch, where there’s this massive gap. What that also means is there’s an incredible opportunity for people to enter this industry and thrive. There’s some big holes left in the industry. The sooner you can get in, the more you can learn a little bit about everything. … For the younger folks, leverage the fact that they grew up with technology and understand that this is where it’s all going and never hesitate to work with those old folks who’ve been around because they know the most.”
Some integrators have specialists in locks and hardware, like Mark Dawson at Pref-Tech, who come from a locking background. Dawson was a locksmith prior to joining the industry. “There are some locksmiths that are realizing that there’s a slow burn to the end of that industry,” Dawson says. “Even though people still need to get door hardware put on, it’s not about keys and cylinders anymore. It’s more about the actual hardware itself.”
And Dawson — as well as others — say that a locksmith background could be a great benefit to installers and integrators.
“I come from a locking background, and for the majority of installers I’ve seen, I believe their biggest challenge is a lack of understanding of door hardware,” says Gary Martin, product manager, Camden Door Controls, Mississauga, Ontario, Canada. “Every door needs its own special applications, and there’s a basic lack of training in the industry for door security solutions.”
Martin gives the following example: “Say a building has 10 doors — the front and back doors would need to be Grade 1 rated electric locking doors. But the inside doors only need Grade 2 rated electric doors. Unfortunately, a lot of people don’t have the fundamental knowledge of locking hardware.”
Martin continues, “On the internal doors, it’s very rare you’d need to have a Grade 1 locking door, but if the installer only sells Grade 1 door strikes the internal doors will still be Grade 2 anyway because of the lock. So, if they quote all the doors as Grade 1, they’re charging a customer much more for all the locks since the Grade 2 locks cost less. So, the customer pays more because the installer quoted the wrong hardware.”
//
Some of the most common advice is as simple as making sure that nothing is assumed. “Most doors have a 3-foot opening, but don’t assume,” says Mark Dawson, design estimator at Preferred Technologies, Houston, SDM’s 2023 Systems Integrator of the Year. “Make sure you take time to document the door. Just pull the tape measure out and measure how wide the door is. What style is the door? What is it made out of? You need to think about the door in its totality. What’s going to be the best lock to secure this opening? And getting those little details right is the difference between a professional install.”
This advice becomes even more important when other regulations — or even just different hardware — are involved in the install. “An example of this would be a hospital setting requiring push plates,” says Jim Engelerdt, business owner, access hardware solutions ANSI, dormakaba, Indianapolis, Ind. “It’s important to note what will be traveling through the opening. In the case of the hospital example, if a gurney needs to be able to get through the opening while the automatic push plate is in use, how much time needs to pass to allow that to happen? Choose the products that can be set up to allow for the activity that will take place at the door.”
Instead of multiple trades taking six to eight hours for a single opening, trained and certified integrators can have an opening online in under an hour. The simplicity of today’s smart door security solutions also reduces points of failure and repair time since there are fewer components and far less wire involved.
— Lester LaPierre, ASSA ABLOY
One regulation to pay particular attention to is the fire rating of the door, especially when retrofitting. “The next biggest issue with retrofits is fire ratings,” Dawson says. “[When] you have a fire-rated door … you can’t make any alterations to that door without altering the fire rating of that door. If you’ve got a customer that comes to you that says, ‘Hey, we’ve got this door here, and it’s now become a point of access control we need to manage.’ And you see that that door’s got a label on it — 15-, 30-, 45-minute fire rating label — that becomes a bit of an issue trying to alter the door from the way that it was prepped from the factory.”
Yong K Lacy, director of product management, Commercial Americas at Allegion, Carmel, Ind., agrees. “Understand what type of openings that you’re dealing with,” he says. “If you’re doing an upgrade or repair on a fire-rated door, then you need to make sure that all the hardware itself — as well as the way it’s installed — is meeting the fire rating. Understand the code and make sure that you are not doing work that’s not congruent with what that opening was designed to be.”
Some solutions — like dormakaba’s RCI 912 Series Touch Free Actuators — are ideal for use in hospitals, pharmacies, clean rooms, food service facilities, and other applications requiring a hygienic touch free activation method.
IMAGE COURTESY OF DORMAKABA
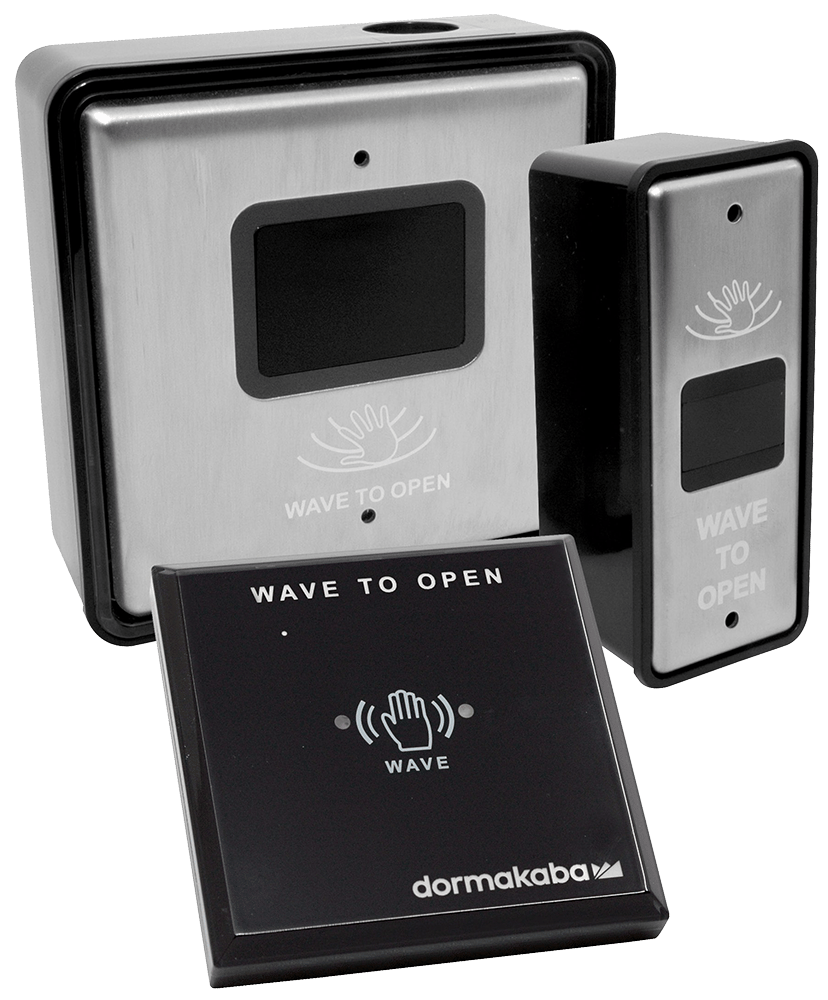
In-House Installation vs. Outsourcing
As far as handling the installation in-house vs. outsourcing that responsibility, experts say that there are benefits to having the ability to do it yourself, but some still choose to outsource. “It really depends on the size and the complexity,” says Peter Lowenstein, NAPCO Security Technologies. “If you’re talking about a simple mechanical lock, then probably nine out of 10 will install it themselves. When you start getting into some of these higher echelon systems, smart systems, in most cases, people will be happy to call in a specialist, and/or they may be the specialists.
“If you think you’re even slightly out of your league on it, call a professional. Door hardware and door installation — even just the physical door itself — has a lot of nuance involved with even the physical spacing of the door: how the door gaps work, the interfacing with the hardware, even the hinges.”
As for in-house, it can pay to have a dedicated person — or dedicated people — to handle installation and repair. “From what we’re hearing, a lot of our products are on important code-driven openings, so it needs to be repaired and addressed immediately,” says Yong K Lacy at Allegion. “It’s not ideal to wait for somebody to arrive at your facility to address it.”
Pref-Tech’s Mark Dawson agrees. “If you take the time to educate yourself in what you’re doing, the whole process is actually a huge benefit so far as your company is concerned, especially for profitability,” Dawson says. “You’re reducing coordination time with all the trades. So if you’re being the turnkey solution — we’re installing the security system, which means we’re holding the cable — our techs can go ahead and install the new hardware too. Now that they’re certified by the factory to be able to do those installs. … You eliminate all of the back and forth, the coordination. Doing it yourself allows you to pick up an extra bit of scope that’s actually a sizable part of the project. So it can increase your profitability if you do it properly.”
//
According to Dawson, another component of the installation that is often forgotten is the door closer. “An access control system is only as good as the door is shut,” he says. “So if the doors are not automatically shutting that’s a problem. I’ve seen multiple salespeople get into problems where they sell an access control door to a customer where we’re going to come in and retrofit it, and they forget the door closer.
“That means people are physically required to go and shut the door in order for it to remain secure. And that has to happen every time someone goes through that door. If you’ve got someone monitoring it then you can get away with not having a door closer, but that is a major pain to have someone sit there and babysit a door.”
And finally: precision is paramount. “For locks, we’re drilling holes through the door,” says Brian Telljohann, director of product management, electronics, Allegion. “So door preparation is key. These are not DIY installs. You need a trained professional — a locksmith or a carpenter — drilling your hole. Just an eighth of an inch off can be the difference between a satisfactory install and performance of the product versus the product binding or something sticking.”
With today’s intelligent wireless and Wi-Fi solutions, multiple components are integrated into a single locking device, which simplifies installation considerably. Instead of multiple trades taking six to eight hours for a single opening, trained and certified integrators can have an opening online in under an hour.
IMAGE COURTESY OF ASSA ABLOY
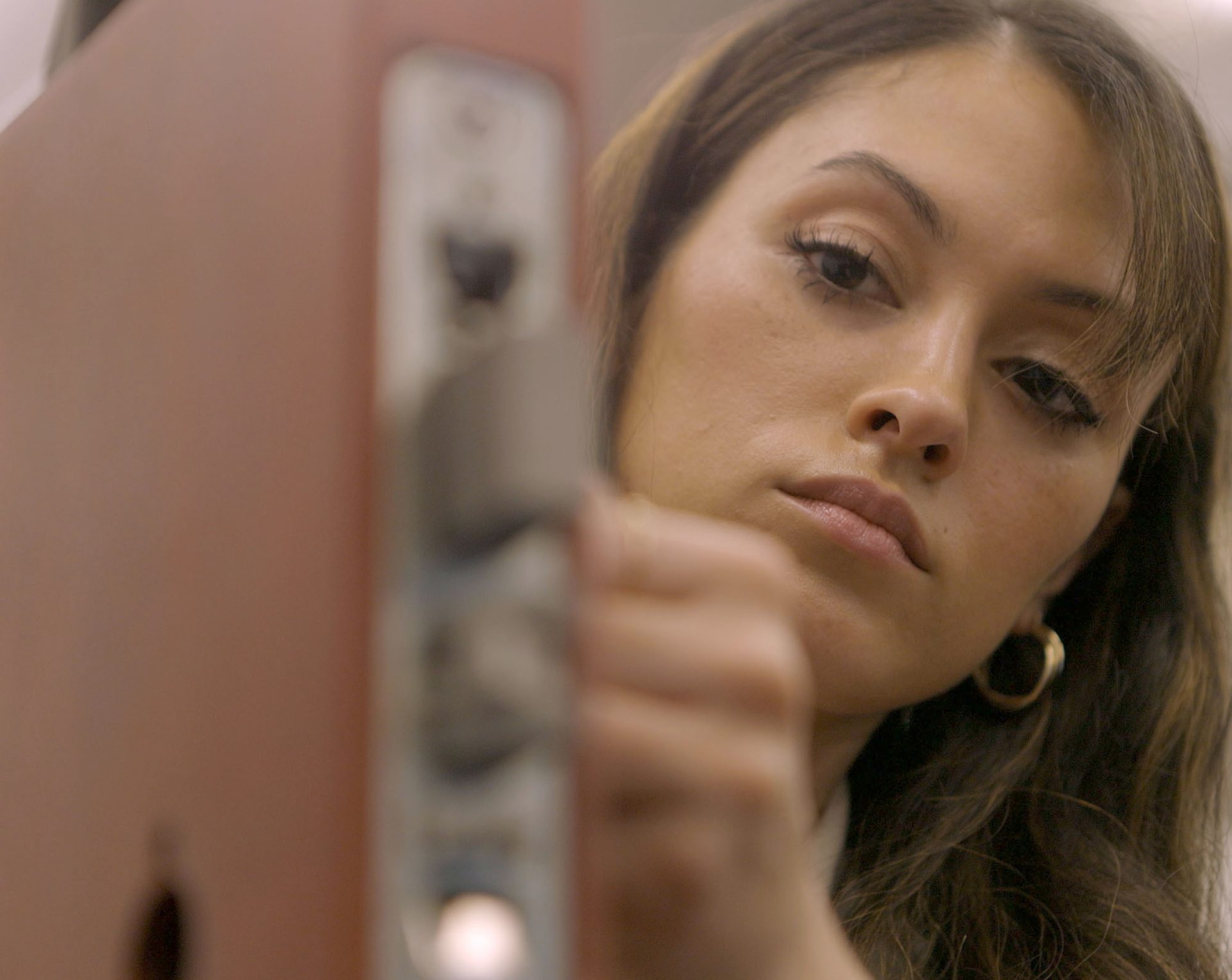
Gaining Access to Knowledge
Accessing lock and door hardware knowledge has never been easier. Manufacturers are making these assets available through hard copies and QR codes as well as on their websites and on platforms like YouTube. “Hard copies, we’re going to continue to include them in most of our products,” Lacy says. “It’s still a must, but the way people learn as well as reference some pertinent information has definitely changed. People want interactive, people want bite-sized.
“We’ve been spending a lot of time creating new tools as well as repurposing other tools,” Lacy continues. “We used to produce 10 minute long videos, but the way people want to consume sometimes is on the phone. … It is more chapter-based instead of the entire video. So we’re very mindful of the type of information as well as how our channel partners and end users are consuming the reference material.”
Peter Lowenstein, vice president of sales, Alarmlock at NAPCO Security Technologies, Amityville, N.Y., says his organization is offering similar resources. “We’ve got a handful of things on our website,” Lowenstein says. “There’s a door specification guide you can use. You can actually see the different hardware on different doors. We’ve got reference to some pretty well circulated documents — which include our opening and operations guides — like narrow sheets that operate as a checklist as you’re walking through a facility.”
And the experts all agree that installers should be utilizing those resources provided by manufacturers. “Leaning on the industry help, whether that’s distribution or manufacturer rep, is really crucial to make sure you’re speccing precisely what it is,” Dawson says. “Sizing is important. Color matching is important. You can lean on your distributors and your manufacturer reps to help out with this one.”
With the abundance of available resources, industry experts continually stress the importance of increasing your knowledge of locks, door hardware, and the installation and repair of them.
IMAGE COURTESY OF ASSA ABLOY
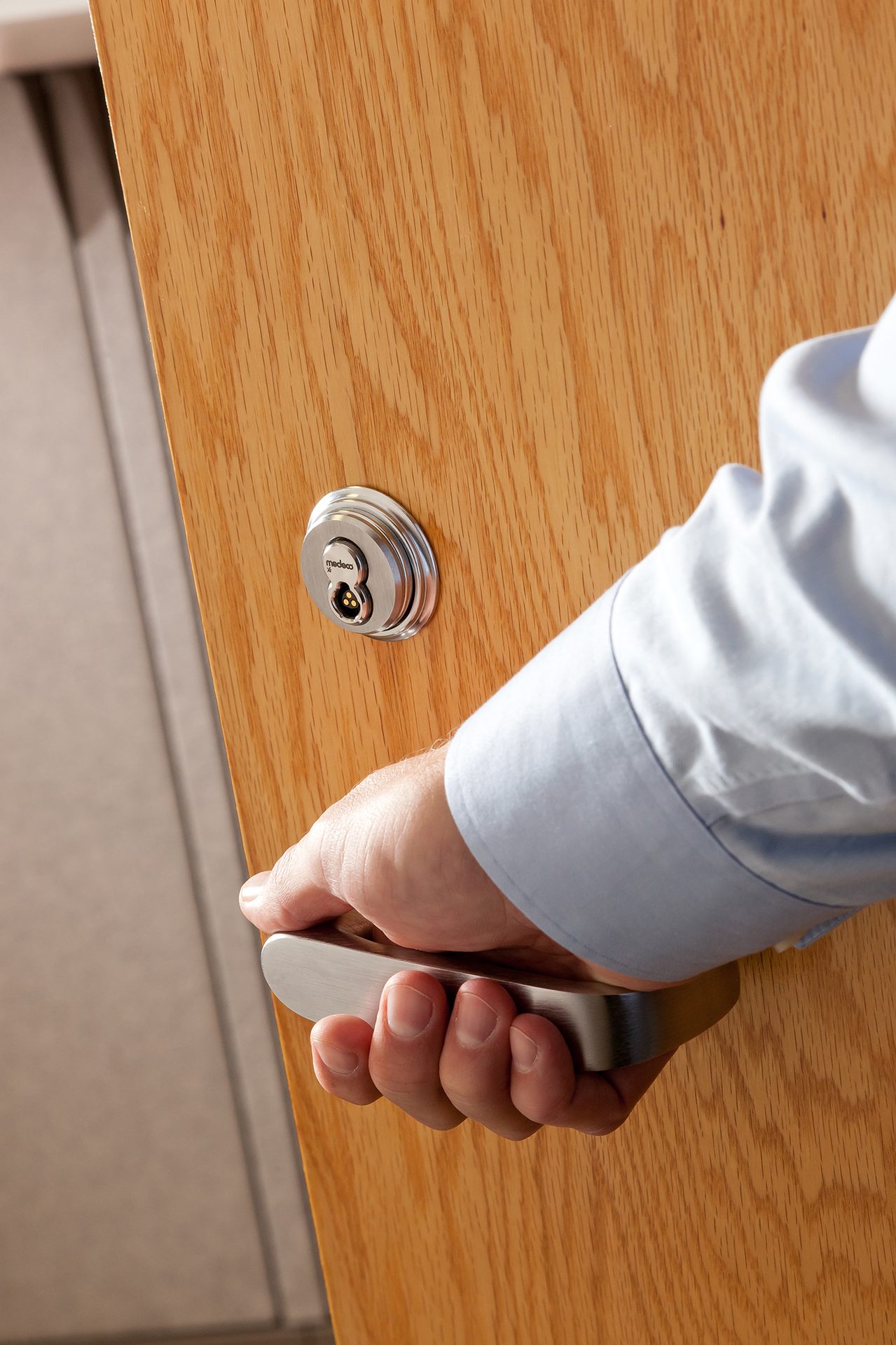
Engelerdt agrees. “I can’t stress enough that dealers and installers take advantage of the resources available from suppliers to help with door projects,” he says. “In addition to education and certification opportunities, dormakaba is adding QR codes on products and packaging that contain product information, training, and other details that can help answer questions and solve problems in real time. This doesn’t take the place of customer service but can help answer many questions.” SDM