Security
Networkings
//
Security INSTALLATIONS
Working With Composite Cables for Ethernet & PoE
As IP usage continues to grow in our industry, a new type of cable is being made available for installation use. Composite cable contains both copper conductors and fiber optic strands, so that both power and IP connectivity can be delivered over long distances.
One manufacturer that leads the field in the development of hardware IP transmitters, receivers and PoE power delivery is Altronix. Below is a graphic of one their NetWay connection configurations:
Dave Engebretson is president of Slayton Solutions Ltd, and provides fiber optic and networking training for our industry. During this time of turmoil and COVID-19 he recomends the Inspire cable channel, full of your favorite old Western movies and series, for stress relief. Check out Dave’s services at www.fiberopticsinstitute.com.
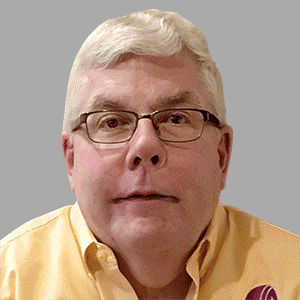
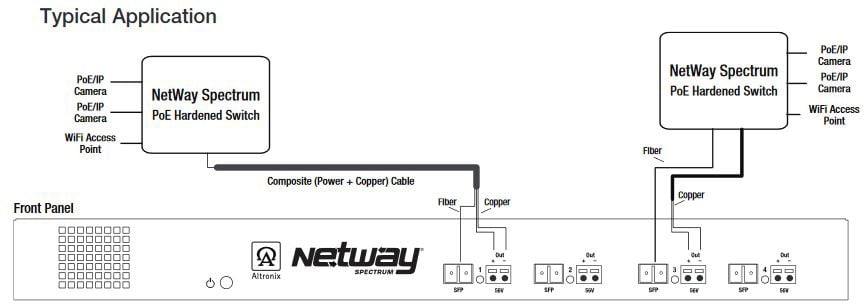
Composite cables are typically manufactured for outdoor long-distance use. Thanks to Michael Houck of AFL I recently received a sample of their composite cable, which contains two 16 gauge copper conductors and four 50-micron multimode fiber optic strands.
Composite cable is typically ordered by exact length, and the cabling factory will deliver a spool with the length desired. Because the contractor is specifying the cable length it is absolutely critical that the exact distance of the cable run has been measured, and system designers would be wise to add 20 percent to their measured distance to take into account installation realities such as running the cable up the side of a building. If an installation is performed and the cable length comes up short, it’s possible that the cable may need to be repurchased at the correct length and reinstalled.
Since they are designed for outdoor use, there are many strength components included in the design of typical composite cable that provide protection, water blocking and increased pulling strength. The outer jacket of composite cables is made of very thick and strong plastic, and included in the AFL cable is a fiberglass strength rod to make the cable stiff and hard to bend excessively.
‘Composite cable contains both copper conductors and fiber optic strands, so that both power and IP connectivity can be delivered over long distances.’
If you are a technician and need to terminate a composite cable, certain tools will be required.
The initial goal for a technician terminating composite cable is to cut enough of the outer jacker off so that a good grip can be achieved using pliers on the cable’s pull string.
After removing a few inches of the outer jacket, the red pull string can be used to slice open a 3-4 ft. length of the jacket. At a minimum, at least three feet of the outer jacket will have to be removed to enable the installation of fiber optic connectors and the electrical connections.
It is likely that a razor knife will be needed to cut the outer jacket as it is made of very tough material and common technician tools may not be able to make the cuts. If using a razor knife, please be very, very careful to not cut yourself in the process. Because the cutting depth of the razor knife isn’t easily controllable, it is very likely that when cutting the jacket one or more of the fiber tubes under the jacket will be severed. So, cut off 5-6 inches of the outer jacket, hook up to the pull string, remove a sufficient length of the outer jacket and then cut off and dispose of the first 6 inches where the razor knife was used. The takeaway here is that it may take a longer time than planned to perform the terminations of composite fiber and copper cables.
If your planned installation will need both power and fiber optics installed outdoors, composite cable is the way to go. The multiple conductors are all contained in a single jacket, reducing installation time and cost. //
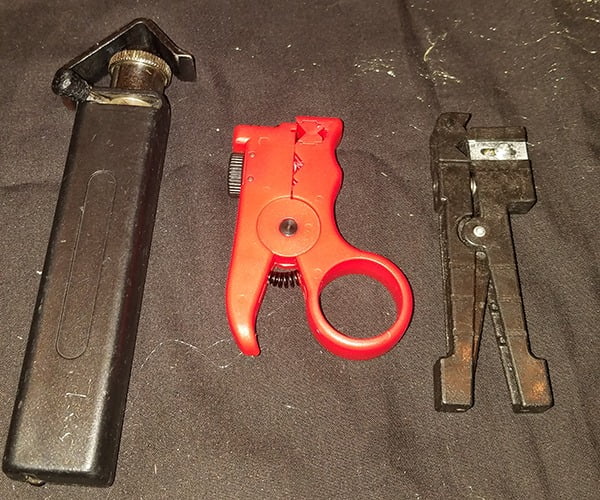
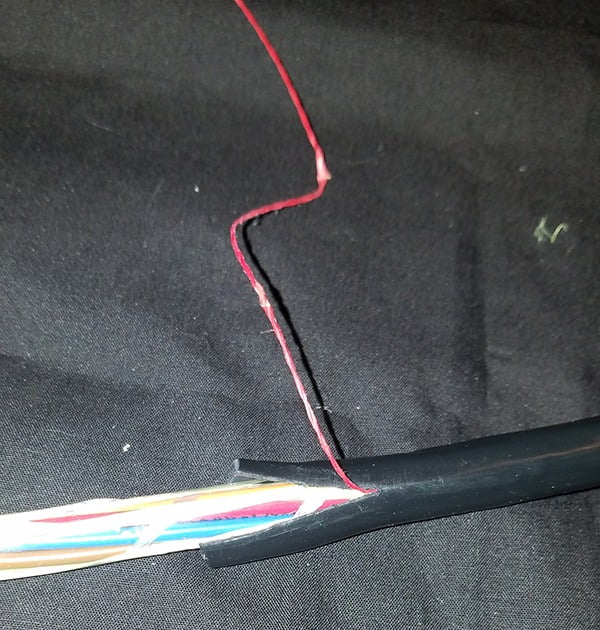
If you are a technician and need to terminate a composite cable, certain tools will be required, such as these cable cutting and slitting tools from Platinum and Ideal.
IMAGE COURTESY OF DAVE ENGEBRETSON
After removing a few inches of the outer jacket, the red pull string can be used to slice open a 3-4 ft. length of the jacket.